Metal injection molding (MIM) is an advanced manufacturing process that allows for the mass production of complex metal components with high precision. However, one of the most significant challenges faced by a metal injection molding manufacturer is the risk of warping and distortion. These defects can compromise the integrity and functionality of the final product, leading to increased production costs and potential performance failures. Understanding the causes and implementing effective preventive measures is essential to maintaining quality and consistency in MIM production.
Key Factors Leading To Warping And Distortion
1. Material Selection and Powder Characteristics
The properties of the metal powder used in MIM play a critical role in determining the final product’s stability. A metal injection molding manufacturer should consider the following factors when selecting materials:
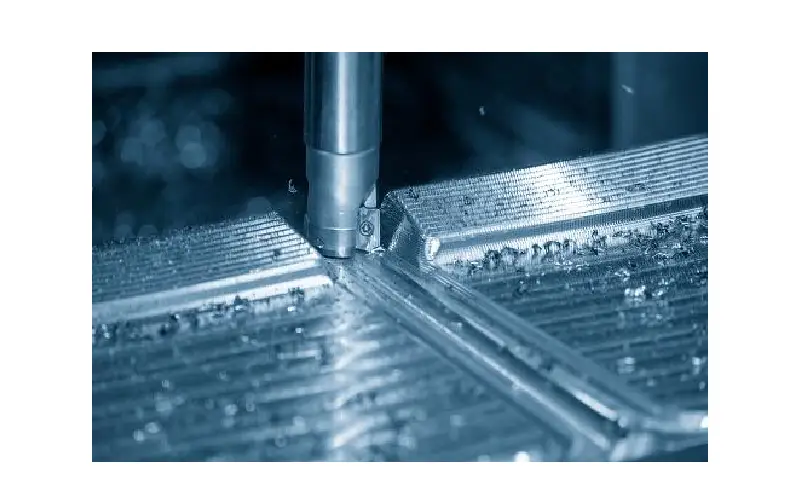
- Particle Size Distribution: Uneven or overly large particle sizes can lead to inconsistent shrinkage rates, increasing the likelihood of warping.
- Binder Composition: The choice of binder influences the debinding and sintering stages. A poorly selected binder system can lead to residual stress, causing distortion.
- Metal Alloy Selection: Different metal alloys exhibit varied thermal expansion and contraction rates. Selecting an alloy with minimal shrinkage variation can help prevent warping.
2. Proper Mold Design and Gate Placement
Mold design is a crucial factor in controlling part distortion. A well-designed mold should consider:
- Uniform Wall Thickness: Uneven wall thickness results in differential cooling rates, leading to warping.
- Strategic Gate Placement: Proper gate positioning helps ensure even material flow, reducing internal stress.
- Draft Angles and Rib Design: Including appropriate draft angles and ribs can enhance structural stability and minimize deformation.
3. Optimizing the Injection Molding Process
To reduce the risk of distortion during injection molding, manufacturers should focus on:
- Injection Pressure and Speed: High pressure or speed can introduce stress in the part, leading to warping.
- Filling and Packing Phases: Proper control over these phases ensures uniform material distribution and minimizes shrinkage variations.
- Controlled Cooling Rate: Rapid cooling causes uneven shrinkage, while controlled cooling ensures dimensional stability.
Understanding Warping And Distortion In MIM
Warping and distortion occur when there is uneven shrinkage or stress distribution in the molded part. These defects can result from multiple factors, including improper material selection, mold design, sintering conditions, and cooling rates. Addressing these issues requires a systematic approach that begins at the design stage and continues through each step of the MIM process.
Debinding: A Critical Stage For Preventing Distortion
The debinding stage involves removing the binder system to prepare the part for sintering. Improper debinding can lead to defects such as:
- Cracking and Deformation: If the binder is removed too quickly, internal stresses may cause warping.
- Inadequate Binder Removal: Residual binder can affect sintering efficiency, leading to inconsistent shrinkage.
- Optimal Debinding Temperature and Time: Following manufacturer guidelines for temperature and duration ensures uniform binder removal, reducing the risk of warping.
Sintering: Ensuring Dimensional Stability
Sintering is the most crucial stage in MIM, where metal particles fuse to form a solid structure. To minimize distortion:
- Uniform Heating and Cooling: Gradual temperature changes prevent differential expansion and contraction.
- Sintering Atmosphere Control: Proper gas flow and environment management help reduce oxidation and stress buildup.
- Fixture Support: Using specialized sintering fixtures helps maintain part geometry and prevents sagging.
Post-Sintering Quality Control Measures
Even with the best preventive measures, some minor warping may occur. A metal injection molding manufacturer should implement post-sintering quality control measures such as:
- Precision Machining: Correcting slight distortions through CNC machining or grinding.
- Dimensional Inspection: Using coordinate measuring machines (CMM) and optical systems to verify part accuracy.
- Heat Treatment: Stress-relief heat treatments can further stabilize the part and reduce residual stress.
Conclusion
Avoiding warping and distortion in metal injection molding requires a comprehensive approach, starting from material selection and mold design to optimized processing techniques and post-sintering quality control. By understanding the root causes and implementing best practices, a metal injection molding manufacturer can enhance product reliability, reduce defects, and improve overall production efficiency. Investing in high-quality equipment, advanced simulation software, and skilled personnel is essential to achieving consistent results and maintaining a competitive edge in the industry.

Greetings, I’m Joan Fuentes, a blogger hailing from a vibrant city in the United States. Embracing my journey as a young man navigating life’s adventures, my blog is a canvas for sharing experiences and insights. From cultural escapades to personal growth, each post reflects the mosaic of life in my urban haven. Join me in unraveling the tapestry of existence through the lens of my unique experiences and perspectives.